はじめに
現場業務が多岐にわたる工場では、作業の見える化と効率的な管理が課題となることが少なくありません。本記事では、工場内の仕事のフローを見える化し、システム化(デジタル化)を導入したことで、業務の効率化と精度向上を実現した成功事例をご紹介します。
概要
クライアント情報
- 業種: 製造業
- 規模: 従業員85名
- 課題: 現場業務の管理がペーパー中心で把握しづらく、生産遅延やミスを改善したい。
背景
- 紙ベースの作業指示書を使用しており、リアルタイムの進捗確認が困難。
- 作業フローの全体像が共有されていないため、工程間での連携が不足。
- 生産データの手入力による記録ミスが多発。
解決策
システム化の内容
- 作業フローの見える化
工程ごとの作業内容と進捗状況を、デジタルダッシュボードでリアルタイムに表示。 - 生産管理システムの導入
各工程での作業指示をシステム上で一元管理し、タブレット端末を活用して現場に配信。 - データ自動収集
IoTセンサーを使用して、稼働データや品質チェック情報を自動的に記録。
使用技術
- 生産管理システム(独自開発)
- IoTセンサー
結果
- 業務効率の向上
- 作業進捗の共有が容易になり、生産遅延が30%削減。
- 従業員の作業負担が軽減され、ミスが40%減少。
- リアルタイムデータの活用
- 工程ごとの稼働状況や不具合箇所が即座に把握可能に。
- 生産スケジュールの精度が向上し、納期遵守率が20%改善。
- コスト削減
- 紙ベースの作業指示書の廃止により、年間約50万円のコスト削減。
- データ分析を活用した作業効率改善により、年間生産コストを15%削減。
クライアントの声
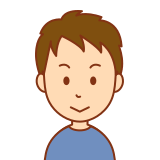
生産管理部長・B様
「システム化により、現場全体が一つのチームとして機能するようになりました。作業の見える化が従業員の意識向上にもつながり、生産性が飛躍的に向上しました。」
システム化のメリット
- 作業の見える化
全工程の進捗がリアルタイムで確認できるため、問題発生時の迅速な対応が可能。 - 生産データの正確性向上
IoTセンサーや自動入力により、データの正確性が大幅に向上。 - 従業員の負担軽減
作業指示やデータ管理が簡素化され、現場スタッフの負担が軽減。 - 組織全体の連携強化
部門間での情報共有がスムーズになり、効率的なチーム運営が可能に。
実現するためのステップ
- 現状分析: 工場内の業務フローを徹底的に調査。
- 課題の特定: ボトルネックや非効率な箇所を洗い出す。
- システム設計: 業務に適した生産管理システムを選定・設計。
- 導入とトレーニング: 現場スタッフへのトレーニングを実施。
- 改善と運用: 継続的な運用と定期的な見直しを行う。
工場の作業フローを見える化し、効率化を目指したい方は、ぜひ当社のソリューションをご検討ください。詳細についてはお問い合わせフォームよりご連絡ください。